Why Apple can’t bring iPhone production to the U.S. and what It would cost us
- The Apple Square
- 2 days ago
- 2 min read
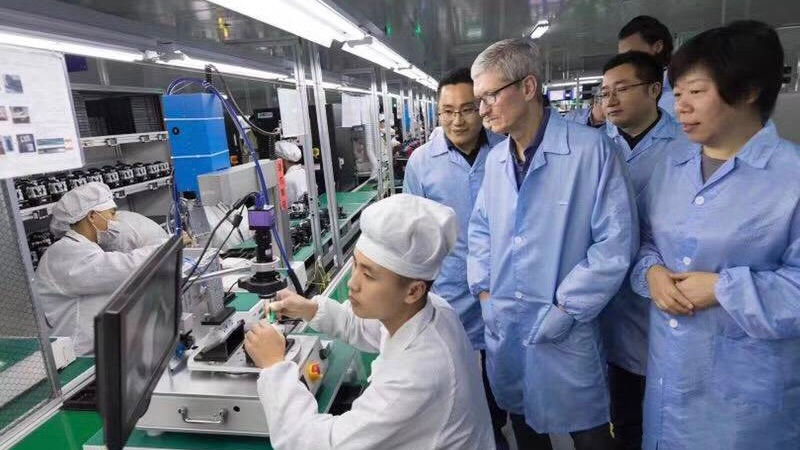
Despite mounting pressure from trade tensions and rising tariffs, Apple has not shifted large-scale iPhone production to the United States—and for good reason. While the idea of “Made in America” appeals to politicians and consumers alike, the reality is far more complex. Building an iPhone in the U.S. would not only disrupt Apple’s supply chain, but also drive up costs for consumers in a dramatic way.
The iPhone is not a product of any one country. It’s a global collaboration, with components sourced from dozens of nations and final assembly concentrated in Asia. Facilities in China and India have been optimized over decades for high-volume manufacturing, with access to skilled labor, established supplier networks, and streamlined logistics. Attempting to replicate that in the U.S. would mean rebuilding the entire ecosystem from the ground up—an expensive and time-consuming endeavor.
Labor costs are one of the most immediate hurdles. In China, a vast labor force supports around-the-clock production at a fraction of U.S. wages. American workers, while highly skilled, would command much higher pay, especially in regions where tech manufacturing is not already established. According to estimates from industry analysts, assembling the iPhone domestically could increase production costs by 30% to 40%, not even accounting for the expense of new infrastructure.
Then there's the issue of scale. Apple’s Chinese partners, like Foxconn and Pegatron, can mobilize hundreds of thousands of workers and manage ultra-fast turnaround times during product launches. No facility in the U.S. currently has the capacity or operational rhythm to match that efficiency. Even if Apple built such plants, it would still need to import most of the parts, which are manufactured overseas—meaning tariffs on components could still apply.
Relocating manufacturing would also slow down Apple’s ability to iterate and innovate quickly. Much of the company’s product development is closely integrated with its assembly lines. Engineers work hand-in-hand with manufacturers during the final stages of design, tweaking materials, tolerances, and finishes in real-time. Splitting this process across continents would add layers of complexity and delay.
The result? iPhones that could cost hundreds of dollars more. Analysts suggest a U.S.-made iPhone might retail for $2,000 or more—well above current pricing. That kind of sticker shock could hurt Apple’s global competitiveness and push more consumers toward rivals that still produce affordably in Asia.
While Apple has made moves to diversify manufacturing—especially with its growing investment in India—it’s unlikely to bring full-scale iPhone production to the U.S. anytime soon. The cost is high, the infrastructure isn’t ready, and the global supply chain isn’t easily untangled. For now, Apple’s strategy remains rooted in balancing production across lower-cost regions while navigating geopolitical pressures as carefully as it designs its devices.